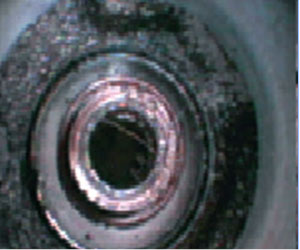 |
|
Video Borescope Inspection
Why use Video-scope inspection on any piece of equipment, because as humans, we rely on our visual sense to make critical decision and video-scope inspection lets you visualize what you normally cannot. We don't have to remove or replace the whole pipe/tube if we can inspect the pipe/tube from the inside and fixed the exact location and make the right decision.
|
|
There are few advantages of this inspection system
-
Identify possible visualized defect (Poor weld root, pitting, scaling, corrosion, crack, clogging and etc)
-
Observe and categorize the extent of each defect
-
Evaluate turbine/tube/pipe condition and cleanliness
-
Predict possible breakdown of equipment
-
Evaluate the overall condition of equipment
-
Reduce re-piping and re-tubing cost
|